The impact of coupling wear on the operation of reducers and maintenance methods
Coupling wear can have multiple impacts on the operation of the gearbox. The following is a specific analysis and corresponding maintenance methods:The impact on the operation of the gearbox
Impact on transmission efficiency: After the coupling wears out, there may be asynchronous phenomena between the two shafts connected, resulting in poor power transmission and requiring the gearbox to consume more energy to maintain transmission during operation, thereby reducing transmission efficiency.
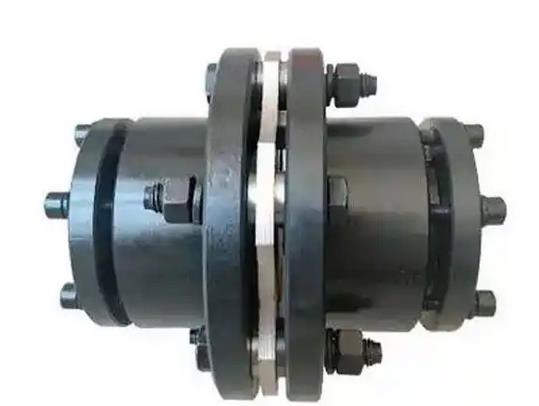
Increased vibration and noise: Wear and tear can cause a decrease in the fitting accuracy of the coupling, resulting in additional vibration and noise during operation. These vibrations and noises not only affect the working environment, but may also further exacerbate the wear of internal components of the gearbox, shortening its service life.
Causing overload and overheating: When the coupling is severely worn, it may slip and fail to transmit the rated torque properly. This will cause the gearbox to bear a load exceeding its design capacity, resulting in motor overload. Long term overload operation can cause severe heating of internal components such as gears and bearings in the gearbox, accelerate the aging of lubricating oil, and affect the normal operation of the gearbox.
Causing damage to the gearbox: Vibration, overload, and other issues caused by coupling wear can subject key components such as gears and shafts inside the gearbox to additional impact and stress. Over the long term, these components may experience fatigue cracks, tooth breakage, and other damages, ultimately leading to the gearbox being unable to function properly.
Maintenance methods
Regular inspection: Develop a regular inspection plan, usually inspecting the coupling at regular intervals (such as weekly or monthly). The inspection includes checking whether the appearance of the coupling is worn, cracked, deformed, etc., whether the connecting bolts are loose, and whether the concentricity and perpendicularity of the coupling meet the requirements. Use professional measuring tools such as dial indicators to check the accuracy of the coupling and promptly identify potential issues.
Correct installation: When installing the coupling, strictly follow the installation instructions to ensure that the coaxiality of the two shafts is within the specified range. Adopt appropriate installation techniques and tools to avoid damage to the coupling during installation. For example, for rigid couplings, the coaxiality error of the two shafts is generally not more than 0.05mm; for elastic couplings, the coaxiality error can be appropriately relaxed, but it should also be controlled within 0.1mm-0.2mm.
Reasonable lubrication: Choose the appropriate lubricant based on the type and working conditions of the coupling. Generally speaking, for high-speed and heavy-duty couplings, lubricating oil with high viscosity and good anti-wear performance should be selected; For low-speed and light load couplings, ordinary lubricating grease can be used. Regularly replenish or replace lubricants to maintain good lubrication of the coupling and reduce wear. For example, for commonly used elastic pin couplings, the lubrication condition should be checked every 2000-3000 hours of operation, and lubricating grease should be replenished or replaced in a timely manner.