How to check the lubrication condition during load debugging of BWY22-43-3KW cycloidal pinwheel reducer
When debugging the load of BWY22-43-3KW cycloidal pinwheel reducer, the lubrication condition can be checked by the following methods:Check the quality of lubricating oil:
Observe color and clarity: Cut off the power, wait for the gearbox to cool down, and then open the oil drain bolt to obtain an oil sample. Normal lubricating oil has a uniform color, clear and transparent. If the oil sample appears cloudy, blackened, contains impurities or has an odor, it indicates that the lubricating oil has deteriorated and needs to be replaced in a timely manner.
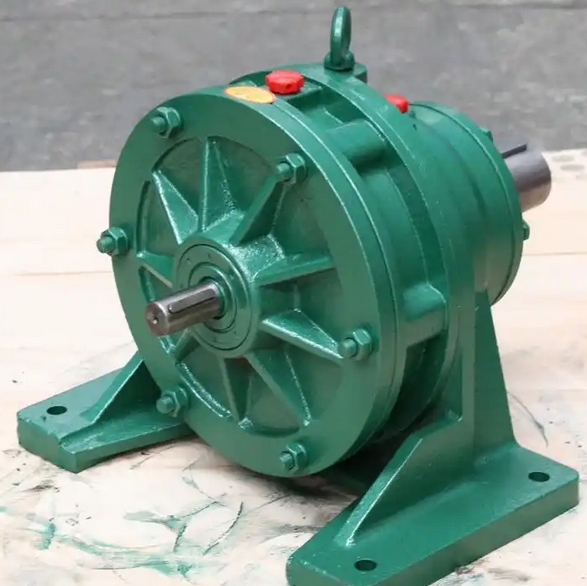
Check for metal debris: The oil sample can be placed on white filter paper for observation. If there are metal debris, it may indicate that there is component wear inside the gearbox and further inspection is needed.
Check the lubricating oil level:
Find the oil level observation device: Cycloid pinwheel reducers usually have oil level observation devices such as oil level plugs, tubular oil gauges, or sight windows.
Shutdown inspection: Cut off the power, wait for the reducer to cool down, remove the oil level plug or check the oil level through a tubular oil gauge or sight glass. The oil level should be within the specified range, for example, the tubular oil gauge should not be less than 2/3 of the oil gauge, and the oil level can be seen in the middle of the sight glass. When stopping the machine, it is generally required that the oil level be between 2/3 of the two scale lines.
Check the lubricator (if any): If the gearbox is equipped with a lubricator, check if it is blocked or damaged. Check if there are impurities accumulating on the filter screen of the lubricator. If so, clean or replace the filter screen in a timely manner; At the same time, check whether the working parts of the lubricator are functioning properly. If any problems are found, repair or replace the lubricator in a timely manner.
Check the lubrication system pipeline: Carefully inspect the lubrication system pipeline, focusing on checking whether there is oil leakage or seepage at the interfaces and connections. Ensure that the pipeline is not damaged or deformed, and that the pipe clamp is firmly fixed. If oil stains are found, the cause should be promptly identified and repaired, such as tightening loose joints, replacing damaged seals, etc.
Check the working pressure and temperature of the lubrication system: The pressure and temperature can be checked by installing pressure gauges and thermometers in the lubrication system. During load debugging, the working pressure and temperature of the lubrication system should be maintained within the normal range. If the pressure is too high or too low, it may indicate problems such as blockage or leakage in the lubrication system; Excessive temperature may cause lubricating oil failure or system malfunction. If any abnormalities are found, the cause should be promptly investigated and resolved.
Check the lubrication of special parts: For cycloidal pinwheel reducers, the arm bearings are the key lubrication parts. During load debugging, it is important to observe the operation of the arm bearings, listen for any abnormal sounds, feel if their temperature is normal, and determine if their lubrication is good. If conditions permit, temperature sensors and other equipment can be used to detect the temperature of the rotating arm bearings to ensure that they are within the normal operating temperature range.