What are the common faults of GRF167-Y37-4P reducer?
The GRF167-Y37-4P reducer may experience the following common faults during use:gear fault
Tooth surface wear: Long term load operation, poor lubrication or oil quality, as well as impurities in the working environment, can gradually wear the gear tooth surface, causing changes in tooth shape and affecting transmission accuracy and efficiency.
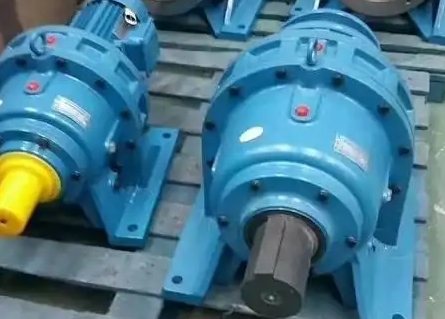
Tooth surface pitting: Under alternating loads, the contact stress on the tooth surface exceeds the fatigue limit of the material, resulting in small fatigue cracks. Over time, the cracks propagate to form pitting pits, damaging the integrity of the tooth surface and causing vibration and noise.
Tooth breakage: Excessive impact load on the gear, stress concentration at the tooth root, or defects in the gear material itself can all cause the gear to break, making the reducer unable to function properly.
bearing failure
Wear and tear: Bearings are subjected to radial and axial loads for a long time, coupled with insufficient lubrication, improper installation, and other reasons, which can easily cause wear on the inner and outer rings and rolling elements of the bearing, increasing the bearing clearance and affecting the rotational accuracy and stability of the shaft.
Fatigue damage: After long-term operation, the rolling elements and raceways inside the bearing will be damaged by fatigue, such as cracks and peeling, resulting in bearing failure and increased vibration and noise of the gearbox.
Sealing issue
Oil leakage: After long-term use, the sealing components may age, deform, or be damaged, causing lubricating oil leakage inside the gearbox. In addition, uneven mating surfaces of the casing, loose bolts, high oil levels, or blocked ventilation holes can also cause oil leakage, which not only pollutes the environment but also affects the normal lubrication and heat dissipation of the gearbox.
Abnormal fever
Overloading: If the actual load borne by the reducer exceeds its rated load, it will cause the motor and reducer to overload, generating excessive heat and causing the temperature of the reducer to rise.
Poor heat dissipation: Installing the reducer in a poorly ventilated area or in an environment with high temperatures can affect its heat dissipation effect. In addition, the accumulation of dust and oil on the surface of the reducer can also hinder heat dissipation.
Lubrication problem: Insufficient lubricating oil, poor oil quality, or lubrication system failure can cause increased friction between components such as gears and bearings, generating a large amount of heat and causing abnormal heating of the gearbox.
vibration and noise
Installation issues: Improper installation of the gearbox, uneven foundation, or misaligned coupling can cause vibration and noise during operation.
Component damage: Gear wear, bearing damage, loose internal components, etc. can disrupt the smooth operation of the gearbox, leading to increased vibration and noise.
Motor failure: Motor imbalance, winding short circuit, rotor bar breakage and other faults can also be transmitted to the reducer through the coupling, causing vibration and noise.
Output shaft malfunction
Wear and tear: The connection parts between the output shaft, coupling, and working machinery are prone to wear and tear due to long-term torque and axial force, resulting in a decrease in fitting accuracy and affecting power transmission.
Deformation: If the output shaft is subjected to excessive radial force or impact load, deformation may occur, causing the axis of rotation of the shaft to be non parallel to other components, resulting in unstable equipment operation.