How to choose the appropriate heat treatment method for gear reducers in practical applications
In practical applications, selecting the appropriate heat treatment method for the gearbox body requires comprehensive consideration of factors such as materials, working conditions, and performance requirements. The following are specific selection methods:According to material selection: If the box material is medium carbon steel or medium carbon alloy steel, such as 45 steel, 40Cr, etc., quenching, tempering, normalizing and other heat treatment methods can be used to improve strength and hardness; For low carbon steel, such as 20 steel, carburizing and quenching are commonly used methods to achieve high hardness and wear resistance on the surface, while maintaining good toughness in the core; For some high-precision and low deformation box bodies, nitriding treatment may be used, which is suitable for medium carbon steel and alloy steel parts.
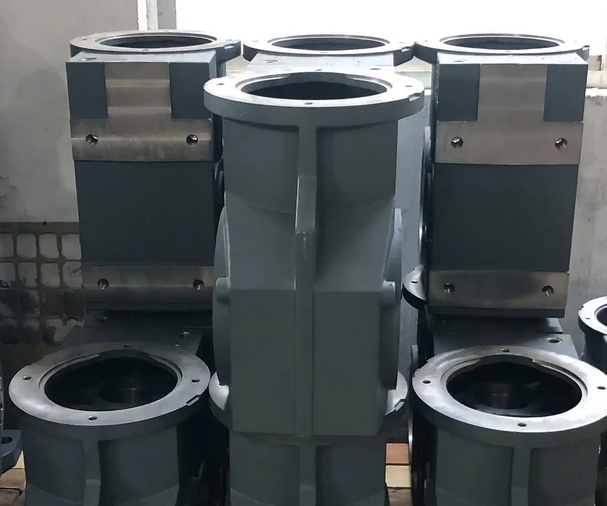
According to the working conditions, if the gear reducer housing is under low-speed, light load, and non impact working conditions, stress relief annealing can be used to eliminate internal stress and improve the cutting performance of the material; For low-speed and medium load situations, quenching and tempering treatment can be used to obtain good comprehensive mechanical properties; When working under conditions of medium speed, medium load, low speed, and heavy load without violent impact, quenching and tempering or normalizing can be used, followed by induction heating surface quenching and low-temperature tempering to improve surface hardness and wear resistance; For working conditions with high speed, heavy load, and impact, such as automotive transmission gears, carburizing, quenching, and low-temperature tempering are usually used to improve the hardness, wear resistance, and impact resistance of the gears.
According to performance requirements, if the box body is required to have high hardness and wear resistance, quenching or surface quenching treatment can be chosen. The commonly used methods for surface quenching include high-frequency quenching and flame quenching. High frequency quenching is suitable for small-sized gears, while flame quenching is suitable for large-sized gears. If the box needs to achieve high hardness and wear resistance with minimal deformation, nitriding treatment can be used, and generally no further precision machining is required after nitriding. If you want to improve the comprehensive mechanical properties of the box, quenching and tempering treatment can be carried out, that is, high-temperature tempering after quenching, so that the box has both certain strength and hardness, as well as good toughness.
According to the type of gear, for hard tooth gears, carburizing quenching or nitriding treatment is often used to improve the hardness and wear resistance of the tooth surface; For soft tooth surface gears, methods such as normalizing and tempering can be used to adjust hardness and toughness. When the meshing gears have soft tooth surfaces, the hardness of the tooth surface of the small gear should be greater than that of the large gear; When both the large and small gears have hard tooth surfaces and high hardness, the hardness of the two gears can be the same.