In addition to the aforementioned measures, what other methods can be used to improve the performance of the ZQH250-16.46-1 gear reducer?
In addition to the measures mentioned above to improve the working environment, the performance of gear reducers can also be improved through optimizing design, improving manufacturing and assembly accuracy, and improving lubrication, as follows:Optimize gear design
Choose the appropriate tooth profile: In addition to the common involute tooth profile, the involute tooth profile or circular arc tooth profile can be modified according to the working conditions to reduce meshing friction and energy loss.
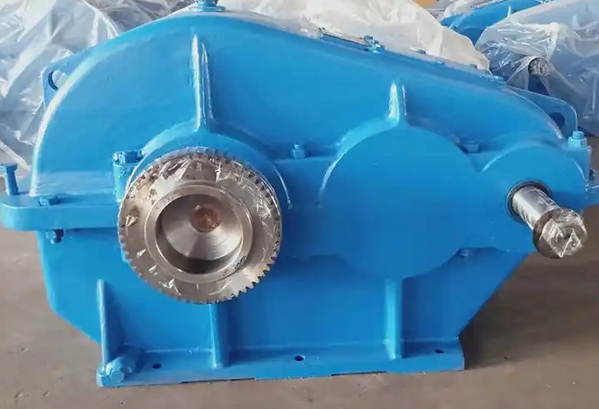
Reasonably determine parameters: Increasing the modulus and pressure angle appropriately can improve the gear load capacity, while considering the impact on transmission efficiency comprehensively. Reasonably choose the gear ratio to avoid increasing energy loss due to improper gear ratio.
Increasing tooth width: When the outer diameter is constant, appropriately increasing the gear width can increase the load-bearing capacity and reduce the constant torque under unit load.
Improve manufacturing and assembly accuracy
Control machining errors: Strictly control tooth profile errors, tooth pitch errors, tooth orientation errors, etc., to ensure accurate and stable gear meshing. High precision machining equipment and measuring tools can be used.
Ensure installation accuracy: During assembly, ensure the parallelism, coaxiality, and center distance accuracy of the gear shaft, so that the gears mesh well and avoid eccentric load and local wear. Through precise assembly processes, the meshing between gears can be made tighter, reducing clearances.
Selecting appropriate materials and heat treatment
Choosing high-quality materials: High strength alloy steel and other high-quality materials are selected, which have good mechanical properties and wear resistance, can reduce weight, and minimize inertia loss during operation.
Proper heat treatment: By using carburizing quenching, nitriding and other heat treatment processes, the surface hardness and core toughness of the gear are improved, the load-bearing capacity and wear resistance are enhanced, and friction losses are reduced.
Optimize lubrication system
Choose the appropriate lubricant: Based on transmission speed, load, working temperature and other conditions, choose the appropriate lubricating oil or grease to ensure good lubrication effect and reduce friction.
Improved lubrication method: Oil spray lubrication, oil bath lubrication, and other methods can be used to ensure sufficient lubrication of the gears, while avoiding excessive lubrication causing oil mixing loss.
Adopting shock absorption and anti vibration design
Increase structural rigidity: Strengthen the gearbox structure, improve its rigidity, make it less prone to deformation during operation, and reduce the impact of vibration on gear meshing accuracy.
Using shock-absorbing components: Flexible couplings or shock-absorbing materials are used to absorb vibrations caused by external loads, reduce backlash, and extend service life.
Integrated intelligent control system
Building a closed-loop feedback system: Combining precision servo systems and high-precision torque sensors to monitor dynamic torque in real-time and achieve precise loading.
Application of automation control algorithms: By using PLC or other intelligent control systems, the operating parameters of the gearbox are automatically adjusted to adapt to different working conditions and load requirements.