What methods can be used to address the poor gear meshing issue with the ZLY224-9-I hardened gear reducer?
Here are some methods to solve the problem of poor gear meshing in ZLY224-9-I hard tooth surface gear reducer:1. Adjust installation accuracy:
Check the concentricity of the shaft system: Use a dial gauge to measure the radial runout of the gear shaft, ensuring that the concentricity between each shaft is within the specified range. If it exceeds the tolerance, the installation position of the shaft system needs to be adjusted to achieve a higher concentricity requirement to ensure correct gear meshing.
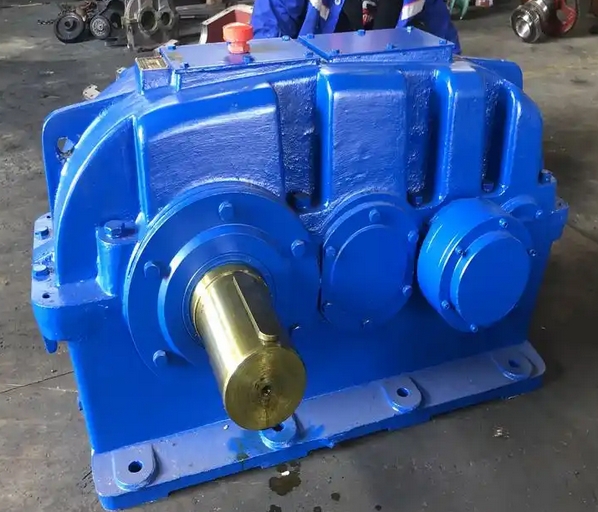
Calibrate the coaxiality of the coupling: Use tools such as laser alignment instruments to adjust the coaxiality of the coupling, avoiding the deviation of the gearbox input and output shafts caused by different shafts of the coupling, which may affect gear meshing.
Adjust bearing clearance: Adjust the bearing clearance axially by locking the nut or other methods to meet the equipment requirements. Appropriate bearing clearance can ensure the stability of gears during operation and reduce gear meshing deviation caused by bearing problems.
2. Repair or replace gears:
Minor wear treatment: For cases of slight wear on the tooth surface, the method of grinding the tooth surface can be used for repair, while replacing the lubricating oil. It is recommended to use extreme pressure gear oil, such as L-CKC 320, to improve the contact condition of the tooth surface.
Moderate wear repair: If the tooth surface wear reaches a moderate level, welding (nickel based welding rod) or laser cladding methods can be used for repair. After repair, the teeth need to be ground to a precision level of 6 or above to restore the correct tooth profile and meshing accuracy of the gear.
Severe wear and broken teeth replacement: When gears are severely worn or broken teeth occur, gear pairs must be replaced in pairs to avoid more serious problems caused by insufficient meshing accuracy between new and old gears. When installing a new gear, it is necessary to calibrate the meshing contact spot, which should be ≥ 70% along the tooth length and ≥ 50% along the tooth height.
3. Optimize lubrication system:
Ensure oil quality and quantity: Use lubricating oil of the required specifications in the instruction manual and replace it regularly. If oil deterioration, water ingress, or impurities exceeding NAS level 9 are found, new oil should be replaced promptly and thoroughly. At the same time, it is necessary to ensure that the oil level is within the normal range and that the oil level does not exceed the centerline of the window during shutdown.
Strengthen oil filtration: Magnetic plugs can be used in the oil tank to adsorb metal particles in the lubricating oil and reduce their damage to the tooth surface. You can also use an oil filter (accuracy ≤ 10 μ m) to filter the oil, keep it clean, and prevent impurities from entering the gear meshing area, which may affect the meshing effect.