What issues should be noted during the use of R117 gearbox?
During the use of R117 gearbox, extra attention should be paid to installation, lubrication, maintenance and other aspects to ensure its normal operation and extend its service life. The following are specific precautions: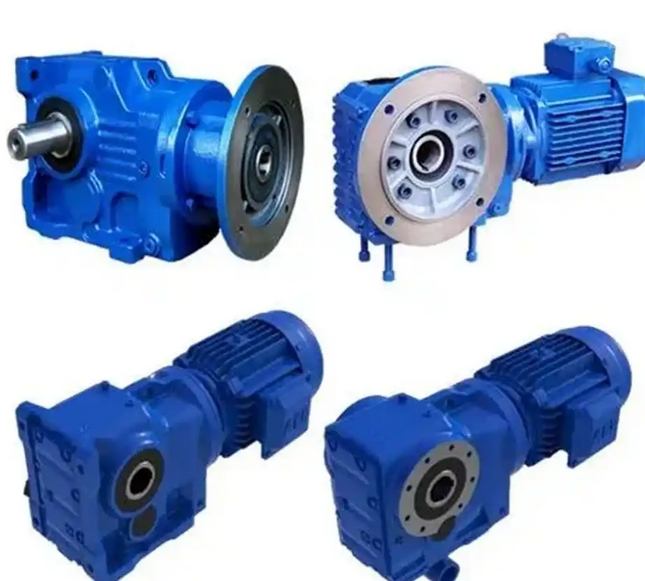
Installation aspect
Basic fixation: The reducer should be installed on a solid and flat foundation to ensure that the foundation can withstand the load and vibration during the operation of the reducer. Use anchor bolts to firmly fix the gearbox on the foundation to prevent displacement or vibration during operation, which may affect its performance and lifespan.
Connection accuracy: The connection with equipment such as motors and working machines must ensure accuracy. When using couplings for connection, the coaxiality of the two shafts must be strictly controlled, otherwise it will increase the load on the internal gears and bearings of the reducer, leading to premature wear or even damage.
Installation space: Adequate installation space should be reserved for subsequent maintenance, inspection, and heat dissipation. The surrounding environment should be kept clean and installation should be avoided in places with dust, water vapor, and corrosive gases.
Lubrication aspect
Lubricating oil selection: Choose the appropriate lubricating oil according to the requirements and working environment of the reducer. Generally speaking, R117 reducers often use medium load industrial gear oils, such as L-CKC series. For reducers working under special conditions such as high temperature and high load, it may be necessary to choose lubricating oil with special properties, such as high temperature resistant and extreme pressure resistant oil.
Oil level inspection: Regularly check the oil level of the gearbox to ensure that the oil level is within the normal range. Excessive oil level can cause an increase in oil temperature, poor heat dissipation, and may also lead to oil leakage; If the oil level is too low, it will cause insufficient lubrication of components such as gears and bearings, accelerating wear.
Oil change cycle: According to the user manual of the reducer, regularly change the lubricating oil. In general, a new gearbox should undergo its first oil change after running for 200-300 hours, and then change the lubricating oil every 5000-10000 hours or annually to ensure the cleanliness and performance of the lubricating oil.
In terms of operation and maintenance
Temperature monitoring: Pay close attention to the temperature changes during the operation of the gearbox. The normal operating temperature is generally between 30-70 ℃. If the temperature is too high, it may be caused by excessive load, poor lubrication, poor heat dissipation, etc. It is necessary to stop the machine in time for inspection and troubleshooting to avoid damaging the equipment.
Noise and vibration: The gearbox should operate smoothly with minimal noise and vibration. If abnormal noise or vibration occurs, it may be caused by gear wear, bearing damage, loose connections, etc., and the machine should be stopped immediately for maintenance to prevent the fault from further expanding.
Load control: Use the reducer strictly according to its rated load to avoid overloading operation. Short term overloading may lead to excessive wear of internal components of the gearbox, while long-term overloading can seriously shorten the service life of the gearbox and even cause equipment failure.
Regular inspection: Conduct a comprehensive inspection of the gearbox regularly, including the tightening of bolts, the sealing performance of seals, and the wear of gears and bearings. Identify and promptly address issues, such as replacing worn parts, tightening loose bolts, replacing aging seals, etc.