What are the possible reasons for the decrease in efficiency of ZD15-4.5-2 soft tooth surface reducer
ZD15-4.5-2 the decrease in efficiency of soft tooth surface reducers may be caused by the following reasons:Gear wear
Tooth surface wear: During long-term operation, there is relative sliding and rolling between gear teeth, which can cause frictional wear. When lubrication is insufficient or oil quality is poor, wear will intensify, causing an increase in tooth surface roughness, a decrease in meshing accuracy, an increase in energy loss, and a decrease in efficiency.
Tooth profile damage: If the gearbox is subjected to excessive load or impact load, it may cause deformation, breakage, and other damage to the gear tooth profile. This will deteriorate the meshing state of the gears, make the transmission unstable, and thus reduce the transmission efficiency.
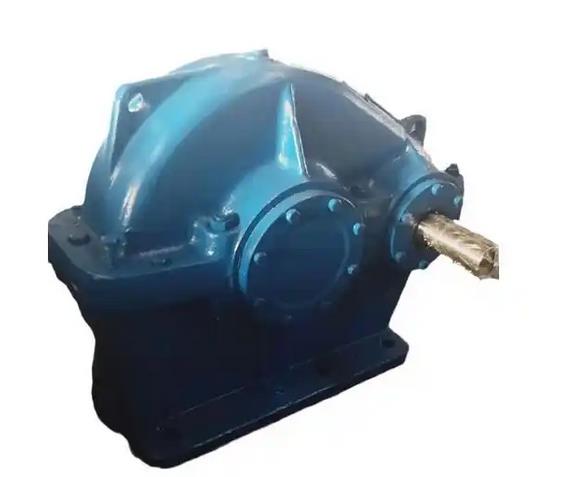
Bearing damage
Bearings are key components that support gear shafts. If bearings experience wear, fatigue pitting, or damage, it will increase frictional resistance and reduce the flexibility of rotating components. This not only leads to additional energy loss, but may also affect the meshing accuracy of the gears, thereby reducing the efficiency of the gearbox.
Lubrication issues
Insufficient lubricating oil: Adequate lubricating oil is crucial for the normal operation of the gearbox. Insufficient oil can lead to insufficient lubrication of components such as gears and bearings, resulting in boundary friction or dry friction, significantly increasing friction losses and reducing efficiency.
Lubricating oil deterioration: After long-term use, lubricating oil will deteriorate due to oxidation, pollution, high temperature, and other reasons. The viscosity, lubrication performance, and heat dissipation performance of deteriorated lubricating oil will decrease, making it unable to effectively lubricate and dissipate heat, resulting in increased internal friction, temperature rise, and reduced efficiency in the gearbox.
Improper lubrication method: Different types and specifications of reducers require appropriate lubrication methods. If the lubrication method is chosen improperly, such as using oil bath lubrication with too high or too low oil level, or poor splashing effect during splash lubrication, it may affect the lubrication effect and lead to a decrease in efficiency.
Sealing issue
Poor sealing of the gearbox can lead to lubricating oil leakage, causing the oil level to drop and affecting the lubrication effect. At the same time, external dust, impurities, etc. may enter the interior of the gearbox, contaminate the lubricating oil, intensify the wear of gears and bearings, and thereby reduce efficiency.
Installation and debugging issues
Insufficient installation accuracy: When installing the reducer, if the installation accuracy does not meet the requirements, such as excessive errors in the coaxiality and parallelism of the gear shaft, it will cause poor gear meshing, uneven load, increase local wear and energy loss, and reduce efficiency.
Unstable foundation: When the reducer is installed on an unstable foundation, it will generate vibration during operation, which will cause additional dynamic loads on components such as gears and bearings, accelerate wear, and affect transmission efficiency.
Work environment issues
High temperature environment: If the working environment temperature of the reducer is too high, it will reduce the viscosity of the lubricating oil, decrease the lubrication performance, and also intensify the thermal expansion of the internal components of the reducer, affecting the meshing clearance of the gears and the clearance of the bearings, resulting in a decrease in efficiency.
Dust environment: In a dusty working environment, dust easily enters the interior of the gearbox, pollutes the lubricating oil, wears down the surfaces of gears and bearings, increases friction loss, and reduces efficiency.