How to solve excessive vibration during load debugging of BLED121-493-0.75KW cycloidal pinwheel reducer
BLED121-493-0.75KW cycloidal reducer experiences excessive vibration during load debugging. The following methods can be used to solve the problem:Installation and connection aspects
Tighten the anchor bolts: Check if the anchor bolts are loose. If they are loose, use appropriate tools to tighten them to the specified torque. If necessary, add elastic washers or use double nuts to prevent the bolts from loosening again.
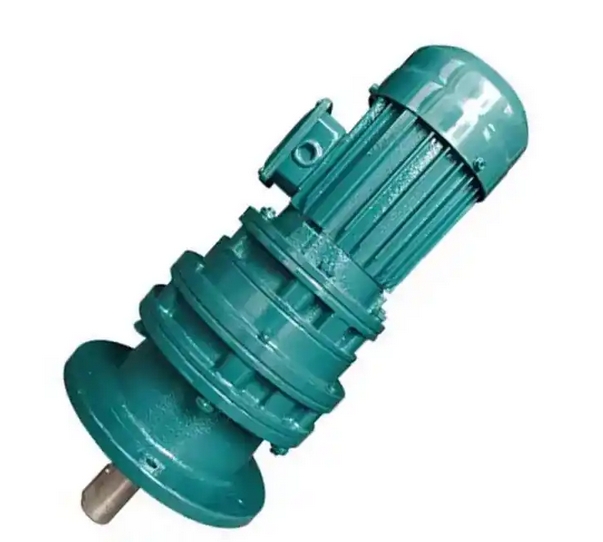
Check the coupling: Check if the coupling is installed correctly and if the pins are worn. If the installation is not correct, it needs to be reinstalled to ensure that the reducer and the shaft of the connected equipment are in a coaxial state; If the column pin is worn out too much, it should be replaced in a timely manner.
Ensure stable installation of the motor: Check if the motor screws are tightened, and tighten them if they are loose. If the installation plane of the motor is uneven, it needs to be repaired or shims added to maintain a good connection between the motor and the reducer.
In terms of internal components
Check the gear: Check whether the gear has tooth surface wear, adhesion, pitting, wear deviation, protrusion, broken teeth, etc., and whether the fit between the gear and the shaft is good. For gears with severe wear and tear, they need to be replaced in a timely manner; If there are problems with the fit between the gear and the shaft, such as improper interference fit or loose assembly, the fit tolerance should be adjusted or reassembled to ensure that the connection between the gear and the shaft is firm and concentric.
Check bearings: Check the wear and clearance size of bearings, such as whether the rolling elements of rolling bearings have rough surfaces, whether the fixing frame is damaged, and whether the sliding bearing alloy is worn, worn, or melted. For bearings with excessive wear or damage, they should be replaced in a timely manner; At the same time, it is necessary to adjust the bearing clearance reasonably by increasing or decreasing the gaskets on both ends of the gland, ensuring that the bearing clearance meets the requirements while ensuring the correct meshing of the gears.
Check the shaft: If the shaft is deformed, it needs to be replaced with a new one. At the same time, it is necessary to check the machining accuracy and surface quality of the shaft to ensure that it meets the requirements and avoid vibration of the reducer caused by shaft problems.
In terms of load and working environment
Verify load condition: Confirm whether the load during debugging is within the rated load range of the gearbox. If the load is too large, adjust the load so that it does not exceed the rated bearing capacity of the gearbox; If the load distribution is uneven, it is necessary to readjust the load distribution to ensure its uniformity.
Avoid resonance: Determine the presence of resonance phenomenon through spectral analysis and other methods. If there is, try changing the operating frequency of the gearbox to avoid areas that are close to the natural frequency of the equipment itself or the surrounding environment; Or adjust the installation method of the equipment, change the supporting structure, etc., to change its natural frequency and avoid resonance.
Lubrication aspect: Check the oil level and quality of the lubricating oil to ensure that the amount of lubricating oil is sufficient. If the oil quality is poor or has deteriorated, it should be replaced with lubricating oil that meets the requirements in a timely manner to ensure good lubrication effect and reduce friction and vibration between parts.