How to optimize the structural design of the TY80-11.4-1.5KW reducer to reduce vibration.
Optimizing the structural design of TY80-114-1.5KW reducer to reduce vibration can be achieved by starting from aspects such as gear system, bearings and shaft system, and box structure. The specific methods are as follows:Optimization of gear system
Using helical gears: Replace spur gears with helical gears, and recommend helical gears with a helix angle of ≥ 15 °. This can increase the number of teeth meshing simultaneously, reduce single tooth impact force, make meshing smoother, and effectively reduce vibration.
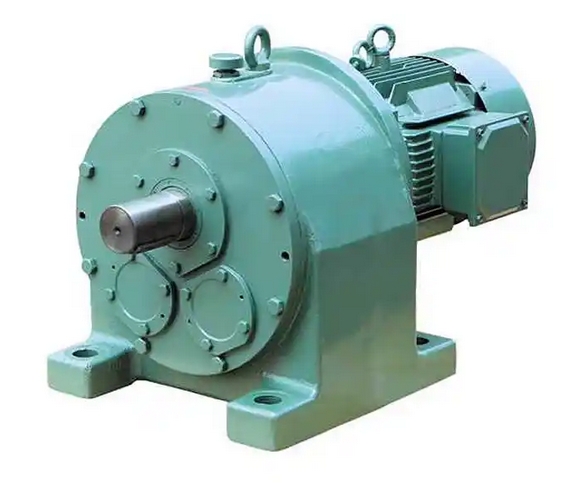
Gear shaping: perform minor modifications such as rounding or bulging on the tooth tips and roots of gears to compensate for elastic deformation and reduce impact and vibration during gear meshing.
Optimize gear parameters: Reasonably select the modulus, number of teeth, pressure angle, and other parameters of the gear. Increasing the number of teeth appropriately can improve the bending strength and load-bearing capacity of the gear, improve transmission performance, and reduce vibration.
Improving machining accuracy: By using precision machining processes such as gear grinding, the gear accuracy is improved to ISO level 5 or above, ensuring low tooth surface roughness, uniform meshing clearance, and reducing vibration caused by manufacturing errors.
Improvement of bearings and shaft systems
Choose low-noise bearings: Use precision rolling bearings such as angular contact ball bearings, cylindrical roller bearings, or liquid dynamic pressure sliding bearings, which use oil film to cushion vibration and reduce noise.
Reasonable design of bearing preload: eliminate axial and radial clearance of the bearing, and avoid impact vibration caused by bearing looseness. The appropriate preload force can be determined through calculation and experimentation, and precisely controlled during assembly.
Optimization of Box Structure
Add reinforcing ribs: Install reinforcing ribs on the box to increase its stiffness, reduce deformation during operation, and suppress vibration propagation.
Design heat dissipation holes: Opening heat dissipation holes at the bottom or other suitable locations of the box can help reduce the temperature of the box and improve the vibration characteristics of the box to a certain extent.
Selecting suitable materials: Using materials with good vibration reduction properties such as gray cast iron or ductile iron to make the box, instead of ordinary steel, can effectively suppress box resonance and reduce vibration.
Optimization of transmission system layout
Adopting symmetrical arrangement: The gear shaft is designed with a symmetrical structure to reduce shaft deformation and vibration caused by eccentricity. At the same time, the rigid box body is used to increase the support stiffness and further enhance stability.
Distributed load: If the total transmission ratio is large, multi-stage deceleration can be used to decompose the total transmission ratio into multiple stages, reducing the load and speed of single-stage gears, thereby reducing vibration.
Add damping components
Installation of elastic coupling: Install polyurethane or other elastic couplings at the input/output ends of the reducer to absorb high-frequency vibration energy and reduce vibration transmission.
Use damping and shock absorption brackets: Add rubber or hydraulic dampers to the installation base to shift the resonance frequency to the non sensitive area and reduce the vibration amplitude.