What are the differences in metallographic structure between DBY450-8-I reducer after carburizing quenching and nitriding treatment
There are various differences in the metallographic structure of DBY450-8-I reducer after carburizing quenching and nitriding treatment, as follows:Differences in phase composition:
Carburizing and quenching: The surface structure is mainly composed of high hardness martensite, residual austenite, and a small amount of carbides. The core is usually composed of low-carbon martensite with good toughness or a structure containing non martensite. The specific structure depends on factors such as steel composition and cooling rate, and ferrite is generally avoided.
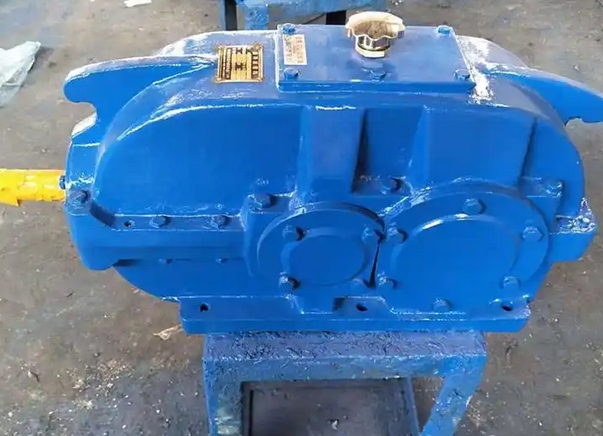
Nitriding treatment: A nitride layer is formed on the surface, such as FeN, CrN, etc. Inside, there is a diffusion layer containing nitrogen, which may contain nitrogen-containing ferrite and other structures. Nitriding treatment generally does not require quenching, and relies on nitrides to improve hardness and wear resistance.
Differences in organizational form:
Carburizing and quenching: The carburizing and quenching temperature is relatively high, and the grain size of the carburizing layer is usually 5-10 μ m. If carburizing is followed by direct quenching, the martensite in the surface layer is acicular, and the low-carbon austenite in the center is transformed into lath martensite. If the carburized material is slowly cooled, a network or sheet-like structure of secondary carbides surrounding dark black pearlite clusters will appear on the surface.
Nitriding treatment: The nitriding temperature is lower, resulting in finer grains that can reach 0.5-1 μ m. The nitrides in the nitride layer are generally dispersed and have a relatively dense structure. They may appear as a bright white layer (nitride layer) and a diffusion layer below, with a relatively uniform diffusion layer structure.
Depth difference of infiltration layer:
Carburizing and quenching: carburizing is generally carried out in the high-temperature austenite zone of 900-950 ℃, with a high diffusion coefficient of carbon atoms, which can quickly form a deep infiltration layer, generally 0.5-2.5mm.
Nitriding treatment: Nitriding is carried out in the ferrite region at 500-570 ℃, with a low diffusion coefficient of nitrogen atoms and a shallow infiltration layer, usually 0.4-0.6mm.
Differences related to hardness:
Carburizing and quenching: The surface hardness is generally around 58-64HRC, corresponding to a hardness value of about 600-700HV.
Nitriding treatment: The surface hardness can reach 700-900HV, and for steel containing Al, Cr, Mo, it can be even higher, reaching 800-1200HV, approximately equivalent to 67-72HRC. Its hardness is significantly higher than that of carburizing and quenching treatment.