What is the difference between the two heat treatment processes of carburizing quenching and nitriding for DBY180-28-3 reducer
The DBY180-28-3 reducer has the following differences between the two heat treatment processes of carburizing, quenching, and nitriding:Different infiltration elements:
Carburizing and quenching: infiltrating carbon elements into the surface layer of steel to form a high carbon surface layer, generally with a carbon content of 0.8% -1.2%. After quenching and low-temperature tempering, the surface layer obtains a high hardness martensitic structure.
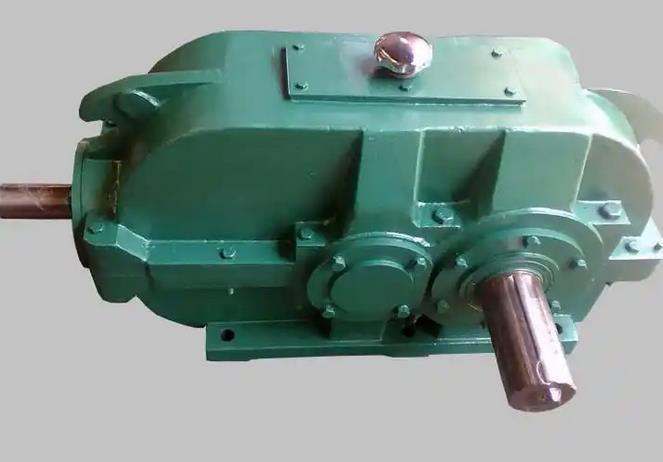
Nitriding: Injecting nitrogen elements into the surface of steel or alloy to form nitrides such as FeN, CrN, etc., which can achieve extremely high hardness without quenching.
Different process temperatures and times:
Carburizing quenching: The temperature is relatively high, usually between 850-950 ℃, and the holding time is relatively long, usually ranging from a few hours to several tens of hours.
Nitriding: The temperature is relatively low, usually between 500-560 ℃, but the insulation time is longer, which may reach tens to tens of hours, or even hundreds of hours.
Different performance characteristics:
Hardness: The surface hardness after nitriding is higher, reaching 950-1200HV; after carburizing and quenching, the hardness is generally 58-64HRC, about 600-700HV.
Wear resistance: Nitriding has better wear resistance than carburizing, especially suitable for situations with low impact and high wear.
Fatigue strength: The nitriding surface forms compressive stress, and the increase in fatigue strength is more significant; Carbonization may generate residual stress due to quenching, and the process needs to be controlled to reduce the risk of cracking.
Deformation: Low nitriding temperature results in minimal deformation of the workpiece; The carburizing temperature is high, and the deformation is relatively large.
Different applicable materials:
Carburizing quenching: mainly used for low-carbon steel or low-carbon alloy steel, such as 20 steel, 20CrMnTi, etc., relying on quenching to achieve hardening.
Nitriding: Suitable for medium carbon steel, alloy structural steel, such as 38CrMoAlA, or alloys containing elements such as Cr, Al, Mo, etc., which can form stable nitrides with nitrogen.
Different application scenarios:
Carburizing and quenching: used for parts that withstand large impact loads and require hard surface and tough core, such as gears, shafts, and other parts in reducers.
Nitriding: Used for parts that require high wear resistance, high precision, and low deformation, such as precision machine tool spindles, valves, molds, etc. If the reducer has extremely high precision requirements, some key parts can be treated with nitriding