How to determine if the vibration of the FAF37-0.55KW-56.4 gearbox housing is caused by poor alignment
To determine whether the vibration of the gearbox body of FAF37-0.55KW-56.4 is caused by poor alignment, the following aspects can be taken into account:Vibration characteristic analysis
Frequency characteristics: Poor alignment usually causes the second harmonic vibration component of the rotor, and the more severe the misalignment, the greater the proportion of the second harmonic component. A vibration spectrum analyzer can be used to detect the vibration of the gearbox housing. If it is found that the amplitude of the second harmonic vibration in the vibration spectrum is large and increases with the increase of speed, and there are even harmonic vibration components such as 2, 4, 6, 8, etc. in the power frequency, it may be caused by poor alignment.
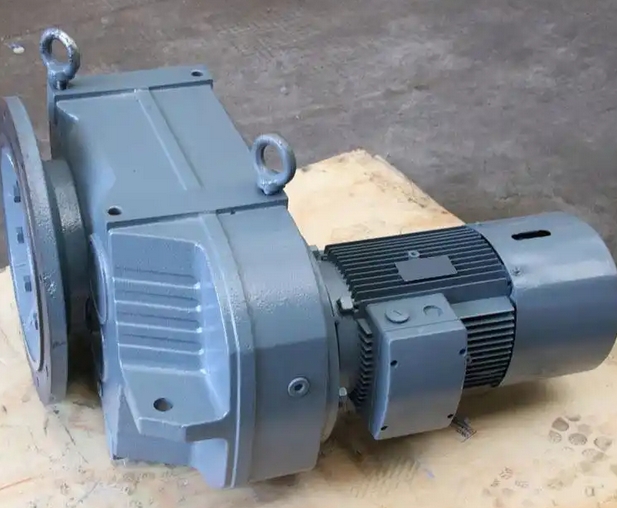
Vibration direction: In general, the bending vibration caused by misalignment is greater in the bending vibration amplitude of bearings near the coupling than in bearings far away from the coupling; And torsional vibration has odd harmonic vibration components such as 1, 3, 5, 7, etc. of the power frequency. At this time, the bending vibration amplitude of the bearing near the coupling is smaller than that of the bearing far away from the coupling.
Equipment inspection
Visual inspection: By directly observing the installation of the gearbox and or other connecting equipment, it is possible to check whether there are obvious signs of displacement, wear, or damage to components such as couplings and connecting bolts. Whether the bolts of the coupling are loose or broken, and whether the connecting surface of the coupling is worn or scratched, these may be caused by abnormal stress due to poor alignment.
Rough measurement with ruler: Use a ruler or other tools to roughly measure the gap between the reducer and the connecting equipment. Under normal circumstances, the gap should be uniform and within a certain range (such as ≤ 0.1mm). If uneven gaps or large deviations are found, it may indicate a problem with alignment.
Professional tool detection: Use professional centering detection tools such as laser centering instruments and dial indicators to accurately measure the coaxiality and perpendicularity between the input shaft of the reducer and the motor shaft, as well as the output shaft and the load shaft. These tools can accurately measure the offset and angular deviation of the axis, thereby determining whether the alignment is good.
Observation of operating status
Temperature changes: Poor alignment can increase the damping inside the coupling, leading to an increase in vibration amplitude, as well as an increase in friction between components, generating more heat. Therefore, if an abnormal increase in temperature is found in the gearbox housing or coupling area, it may be related to poor alignment.
Sound characteristics: During operation, if the gearbox emits periodic abnormal noise, and the noise frequency is related to the speed, it may be caused by poor alignment. Because poor alignment can lead to poor gear meshing and uneven bearing force on the shaft, resulting in abnormal noise. You can use a screwdriver to press against the bearing end while the device is running, and assist in judgment by listening to the sound changes with your ears.
If it is determined through the above methods that the vibration of the gearbox body is caused by poor alignment, timely adjustment and repair should be carried out to avoid further expansion of the fault and affect the normal operation of the equipment.