In addition to installing overload protection devices, what other methods can be used to protect the ZHQ350-48.4-I reducer?
In addition to setting overload protection devices, ZHQ350-48.4-I reducers can also be protected through reasonable selection, regular maintenance, and optimized operating conditions, as follows:Reasonable selection and installation
Correct selection: Based on the actual working load, speed, transmission ratio, and other requirements, choose a suitable specification of reducer to ensure that its rated power and torque can meet the working needs and avoid long-term operation near or exceeding the rated load.
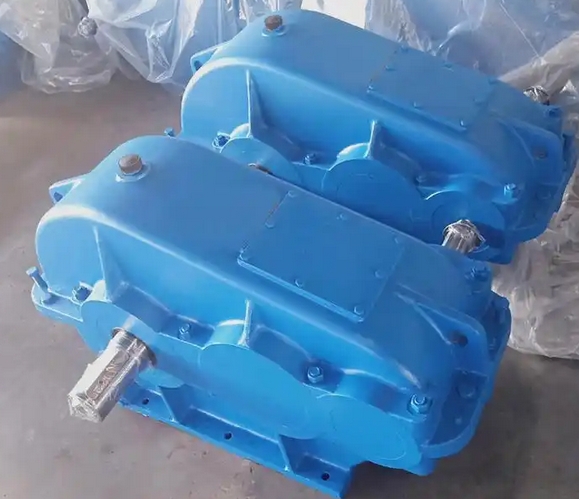
Standardized installation: Strictly follow the installation instructions to ensure the coaxiality of the reducer, motor, working mechanism and other connecting components, and avoid additional stress and wear caused by installation errors. At the same time, the reducer should be firmly installed on a stable and sturdy foundation to prevent vibration and displacement during operation.
Strengthen lubrication management
Choose suitable oil: Select lubricating oil with appropriate viscosity and performance based on the type of reducer, operating temperature, and load conditions, such as heavy-duty gear oil or synthetic oil.
Regularly replace lubricating oil: Replace lubricating oil according to the prescribed cycle, thoroughly drain the old oil when draining, and clean the oil tank and filter to avoid mixing new and old oil and affecting performance. Generally, it should be replaced every six months to one year, depending on the user manual and actual working conditions.
Monitoring oil level and oil condition: Check the oil level weekly or before each start-up to ensure that the oil level is between the upper and lower limits, and replenish it promptly if it is insufficient. Determine whether the lubricating oil has deteriorated through visual inspection, odor, and other methods every month. Conduct oil analysis at least once a year to test viscosity, acid value, and other indicators. If it exceeds the standard, replace it immediately.
Regularly inspect components
Gear inspection: Stop the machine every quarter to check for defects such as wear, pitting, and cracks on the surface of the gear. Use a tooth thickness caliper to measure the degree of wear on the tooth surface. When the wear exceeds 10% -15% of the design value, consider repairing or replacing the gear. Every six months, use a feeler gauge to check the gear mesh clearance, ensuring that the clearance is within the manufacturer's specified range, and tighten the connecting bolts between the gear and the shaft to prevent loosening.
Bearing inspection: Every quarter, check whether the bearing is damaged by listening to sound and touching the temperature, and if necessary, use a vibration detector to detect the vibration value. Disassemble bearings every year, clean and inspect the balls and raceways for wear, and replenish or replace lubricating grease.
Box inspection: Monthly check whether the anchor bolts of the box are loose and whether the foundation is flat. Check if there are cracks or deformations in the box, and repair or replace it promptly if necessary. Check the sealing surfaces of the gearbox for oil leakage every six months and replace aging sealing rings or sealants.